High-capacity shoring solution braces deep basement excavation at new waterfront development
Mirvac needed an efficient basement retention system for a new Brisbane development. Find out why they turned to Coates
The project
Isle is a multistorey residential development currently being constructed by Mirvac in Brisbane’s prestigious Newstead Waterfront precinct. To allow work to begin, Mirvac needed a reliable and cost-effective shoring solution to support the construction of Isle’s 3-storey basement structure. Coates was invited to partner with retention wall specialist, Keller, to deliver a comprehensive internally braced hydraulic retention system.
The challenge
Efficiency
Ground anchors would be in the way of the adjacent Stage 3 building piles which require pre-drilling. They would also have required removal during the excavation of Stage 3. Mirvac required a methodology that would allow for faster installation; avoid the removal and patching of ground anchors; and minimise water ingress through the wall for this and future stages of Newstead Waterfront.
Design capacity
The three braced sides of Isle’s basement structure have high loads and large bracing spans, demanding a shoring solution that utilises large, high-capacity equipment. In addition, the bracing could not be fixed direct to the capping beam due to the reduced levels of the ground level slab, meaning thrust blocks had to be added on top of it.
Site access
Although an internally braced solution was the right choice to safely support the high structural loads for this excavation, ample space was still needed to manoeuvre excavators between the struts. Maintaining sufficient access for loading out material made the excavation methodology one of the biggest design challenges for the project team.
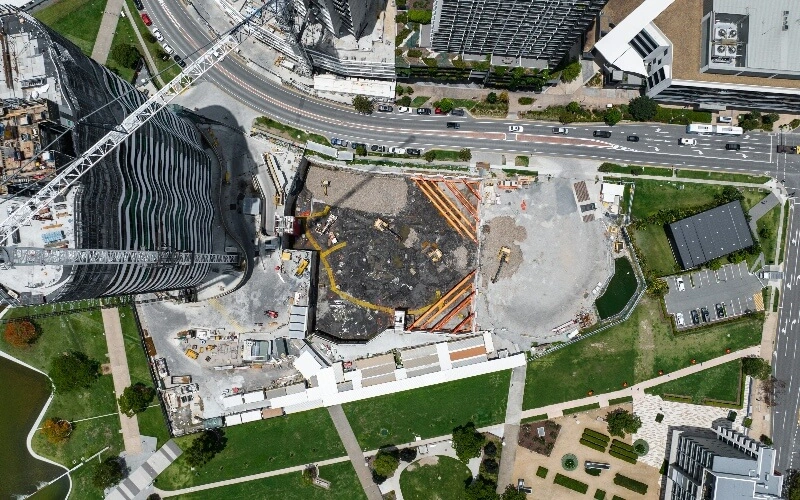
The custom 2-level shoring solution included 14 hydraulic struts
The solution
In July 2023 installation began of a custom 2-level hydraulic shoring solution designed and supplied by Coates, which incorporates:
-
The proprietary HW500 waler system – deployed for the first time for a Coates customer in Queensland
-
A total of 14 hydraulic struts and rams diagonally braced across two corners of the excavation, including: 6 x MP375, 6 x MP250 and 2 x MP150
-
This design places 6 struts on the first basement level and 8 on the second level.
“The innovation that comes with these struts and the new HW500 waler was essential for designing a solution that was both efficient and cost effective for this client,” says Stephen Reghenzani, Coates Temporary Works Engineer.
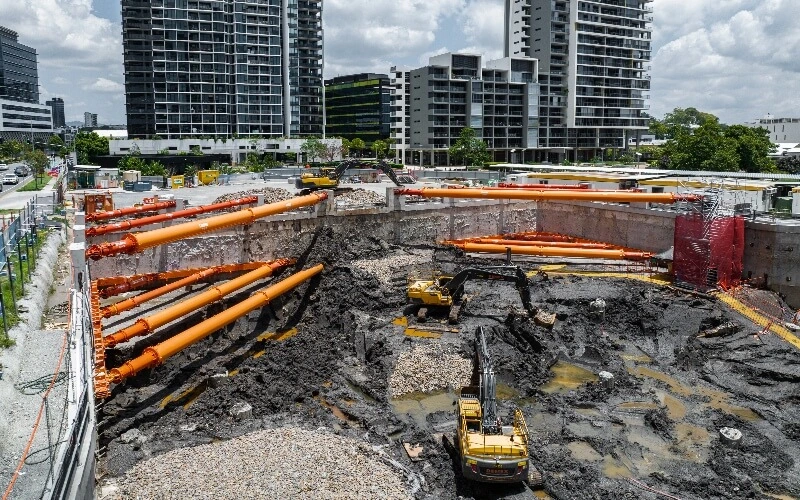
The HW500 waler system was deployed for the first time for a Coates customer in Queensland
The impact
Despite challenges, Mirvac, Coates Engineering Solutions, Keller and consulting engineers ADG Engineers collaborated to design a robust, flexible, cost-effective and minimally invasive retention system, allowing construction to continue safely and to schedule.
Creating space for excavation
Flexibility was important and Coates refined the design based on client feedback to determine the right configuration and location for each of the struts. With excavation nearing completion, Coates’ inhouse engineering team also accommodated new ideas to improve access by temporarily removing one of the lower-level struts.
Managing thermal load
When struts span 25m or more they are subject to thermal loading. With the longest strut for the Isle retention system spanning 29.5m, this was another consideration for the project team. “When the temperature of the struts increases it causes elongation, which increases the resultant load on the strut as it pushes against a stiff retention wall,” Stephen explains. “To combat this, two of the larger MP375 struts were designed to be wrapped with 50mm thick insulation if thermal load limits were reached.”
Safe and secure waler installation
Through effective collaboration, the project team overcame challenges in designing the waler’s attachment to the retention wall. “There were some early concerns about coring into this structure, but we worked extensively as a team to agree on the adjustments that needed to be made,” says Stephen. “These changes included strengthening parts of the retention wall to compensate for the waler attachment.”
Smart safety
Telemetric sensors continue to inform load monitoring throughout basement excavation and construction. “Being able to remotely monitor the forces being applied to the struts and understand the performance of this solution in real time, provides additional assurance for all parties around the safety of this system,” says Stephen.
Sustainable
Traditional anchoring would have meant grouting the pilot holes and stressing the anchors, which means additional water consumption and a dewatering solution to manage surplus water on the site. Coates’ hydraulic solution alleviated the need for these measures. Unlike fabricated steel shoring, this system can also be re-used, further reducing construction waste and improving sustainability.
The removal of temporary works is scheduled for June 2024, when basement construction is complete.
Connect with Coates’ Engineering Solutions to discuss a robust and cost effective temporary works solution for your next project.
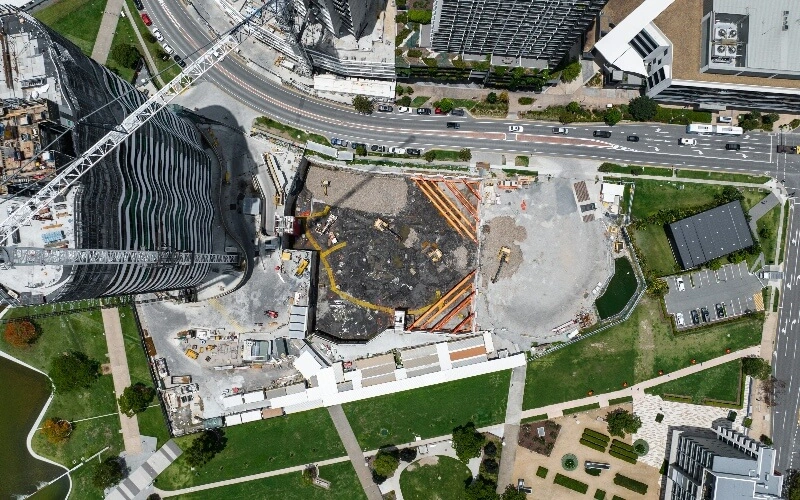
The proprietary HW500 waler system – deployed for the first time for a Coates customer in Queensland
A total of 14 hydraulic struts and rams diagonally braced across two corners of the excavation, including: 6 x MP375, 6 x MP250 and 2 x MP150
This design places 6 struts on the first basement level and 8 on the second level.
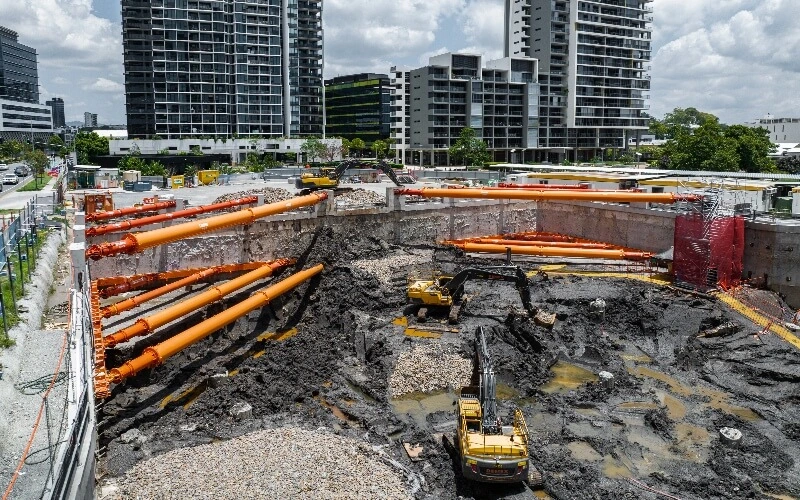